Heat Treatment of Rigging Hardware: Enhancing Performance and Quality
Introduction
Forged rigging hardware, including hooks, shackles, and other lifting components, plays a crucial role in industries like construction, shipping, and heavy machinery. These products must withstand extreme loads, challenging environments, and repeated use. Heat treatment is a key process in ensuring their durability, strength, and reliability.
This blog will explain the fundamentals of heat treatment methods, their effects on rigging hardware performance, and common production challenges. We’ll also explore real-world case studies, cost considerations, testing techniques, and emerging trends in the field.
1. Understanding Heat Treatment Methods
Normalizing
Normalizing involves heating forged rigging hardware to a specified temperature (typically above the material’s critical point) and then air-cooling it. The goal is to refine the grain structure, relieve internal stresses, and improve the material’s uniformity.
Benefits:
- Enhanced toughness and ductility
- Improved machinability
- Reduced stress concentration
Quenching
Quenching is the process of rapidly cooling the material using water, oil, or air after it has been heated. This increases hardness and strength by forming a martensitic structure. However, the cooling rate must be carefully controlled to prevent cracking or distortion.
Common Challenges:
- Risk of cracking or warping
- Internal stress formation
- Inconsistent hardness
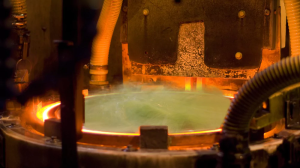
Tempering
After quenching, tempering is used to reduce brittleness while maintaining strength. The metal is reheated to a lower temperature and then cooled. Adjusting the tempering temperature allows manufacturers to balance toughness and hardness according to application needs.
Key Outcomes:
- Reduced brittleness
- Enhanced impact resistance
- Increased flexibility
2. Effects of Heat Treatment on Performance
Heat treatment has a direct impact on the mechanical properties of rigging hardware. Proper treatment ensures products have the strength to withstand heavy loads while maintaining enough toughness to prevent fractures.
- Hardness: Quenching significantly increases hardness, which is essential for wear resistance.
- Toughness: Tempering enhances toughness, making components resistant to cracking.
- Strength: Normalized components exhibit improved structural integrity with balanced strength and ductility.
For instance, hooks subjected to quenching and tempering will possess excellent load-bearing capacity without becoming brittle. Shackles often undergo normalizing to ensure uniform grain structure, which reduces the risk of sudden failure.
3. Common Production Challenges and Solutions
Problem 1: Cracking After Quenching
- Cause: Excessive cooling rate or improper material selection.
- Solution: Adjust the quenching medium or use preheating to reduce thermal stress.
Problem 2: Insufficient Hardness
- Cause: Inadequate quenching temperature or improper cooling time.
- Solution: Verify and maintain the correct quenching temperature based on material composition.
Problem 3: Brittleness After Tempering
- Cause: Over-tempering at high temperatures.
- Solution: Adjust tempering temperature to achieve the desired balance of hardness and toughness.
4. Cost Analysis
Heat treatment costs vary based on factors like energy consumption, equipment, and material handling. While quenching and tempering are more expensive than normalizing, they offer superior performance for high-load applications.
Cost Factors to Consider:
- Energy consumption
- Cooling medium type
- Process cycle time
- Post-treatment testing and inspection
Manufacturers should weigh these costs against the increased longevity and reliability of properly treated hardware to determine the most cost-effective solution.
5. Case Studies
Case Study 1: Shackle Brittleness Issue
A manufacturer encountered frequent shackle fractures. After analyzing the heat treatment records, it was found that the tempering temperature was too low. By increasing the tempering temperature, the toughness improved, reducing failures by 60%.
Case Study 2: Hook Cracking After Quenching
In another instance, a batch of crane hooks exhibited cracks due to rapid water quenching. Switching to oil quenching and adjusting the cooling rate eliminated the issue without compromising hardness.
6. Evaluating Heat Treatment Results
To ensure the effectiveness of heat treatment, various testing methods are used:
- Hardness Testing: Using Rockwell or Brinell hardness testers to measure surface hardness.
- Microstructure Analysis: Microscopic examination to assess grain size and detect defects.
- Impact Testing: Charpy impact tests evaluate material toughness.
- Tensile Testing: Determines yield strength, tensile strength, and elongation.
7. Future Trends in Heat Treatment Of Rigging Hardware
The future of heat treatment is shaped by technological advancements and sustainability efforts:
- Automation and AI: Predictive algorithms optimize heat treatment parameters in real-time.
- Energy Efficiency: Innovations in furnace design reduce energy consumption.
- Advanced Materials: Research on novel alloys with enhanced heat treatment responsiveness.
- Environmentally Friendly Quenching: Water-based quenching solutions minimize environmental impact.
Why Choose Kailipu
At Kailipu, our heat treatment process of quenching and tempering all load-bearing hardware rigging accessories ensures that each accessory achieves the best performance. With strict process controls and advanced testing methods, we guarantee durability, strength, and safety in all our products. Partner with us for reliable rigging solutions designed to meet your toughest demands.
Conclusion
Heat treatment of rigging hardware is a vital process in ensuring the durability, strength, and safety of forged rigging hardware. Understanding the effects of normalizing, quenching, and tempering allows manufacturers to select the appropriate treatment for specific applications.
By addressing production challenges, conducting thorough testing, and staying informed on emerging technologies, companies can enhance product quality while controlling costs.
If you are looking for high-quality and reliable rigging hardware, feel free to contact our team at sales@qd-kailipu.com. Let’s optimize your rigging hardware for peak performance!