Wire Rope Sleeves: Aluminum vs. Copper – Which is Right for Your Application?
When it comes to securing wire ropes in various industries, the right choice of sleeve is crucial. Two popular types of wire rope sleeves, aluminum and copper, offer distinct advantages depending on the application. But how do you know which one is right for your needs? In this article, we’ll break down the key differences between aluminum and copper wire rope sleeves to help you make an informed decision.
Understanding Wire Rope Sleeves
Wire rope sleeves, also known as ferrules, are essential components for creating a secure loop in wire ropes. They are used to terminate or join wire ropes and provide strength, reliability, and safety in applications ranging from construction to maritime operations.
While both aluminum and copper sleeves serve the same basic function, they differ in material properties, strength, and suitability for various applications.
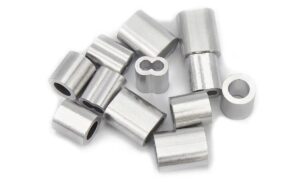
Material and Weight Considerations
Aluminum Sleeves: Made from lightweight aluminum, these sleeves are commonly used in environments where weight is a concern. Aluminum is known for its corrosion resistance, especially in wet and marine settings. For applications where ease of handling and light weight are priorities, aluminum sleeves are a great choice. Industries like adventure parks and marine rigging often favor aluminum for its rust resistance and lightweight properties.
Copper Sleeves: Copper is a heavier, more durable material compared to aluminum. Copper sleeves are typically used in more demanding applications, such as heavy industrial or marine environments where higher loads are involved. Due to their strength and heat resistance, copper sleeves are better suited for high-pressure or high-temperature environments, such as oil and gas or construction industries.
Application Strength
Aluminum Sleeves are often used for lighter-duty applications. They are easy to crimp and install, making them a popular choice for general-purpose rigging where the wire rope doesn’t need to bear extremely heavy loads. However, for critical, high-load applications, aluminum might not provide the necessary strength.
Copper Sleeves are built for heavy-duty use. These sleeves can handle greater stress and higher weights, making them ideal for applications where maximum strength is required. Construction, oil rigs, and industrial sectors often use copper sleeves due to their durability and resistance to wear under pressure.
Corrosion Resistance
Aluminum Sleeves are highly resistant to corrosion, especially in environments exposed to water, such as coastal or marine settings. This makes them a popular choice for maritime applications, where exposure to saltwater can quickly corrode other metals.
Copper Sleeves also offer excellent corrosion resistance, but their ability to resist corrosion is most notable in environments exposed to industrial chemicals or extreme temperatures. Copper is highly durable in these harsh conditions, making it suitable for heavy industrial use.
Cost and Availability
Aluminum Sleeves are typically more affordable and widely available compared to copper sleeves. This makes them a budget-friendly choice for projects where cost is a factor, especially in low to medium-load applications.
Copper Sleeves are generally more expensive due to the material’s higher cost and superior durability. While they may not be as readily available as aluminum sleeves, their higher strength and durability make them worth the investment for heavy-duty applications.
Ease of Installation
Aluminum Sleeves are easy to work with, and they can be swaged (crimped) quickly with hand tools or hydraulic presses. This makes them suitable for projects where frequent adjustments or installations are necessary.
Copper Sleeves, being heavier and stronger, require more force and specialized tools to crimp properly. While they may take more effort to install, their strength and reliability in high-load situations make the extra effort worthwhile.
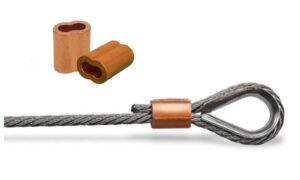
Choosing the Right Wire Rope Sleeve for Your Application
The choice between aluminum and copper wire rope sleeves ultimately comes down to the demands of your application. Here are some factors to consider:
- For lighter-duty applications, such as adventure parks, general rigging, or marine use, aluminum sleeves offer corrosion resistance, light weight, and affordability.
- For heavy-duty applications, where high strength and durability are essential, such as in construction, industrial rigging, or the oil and gas industry, copper sleeves provide superior performance under load.
- For environments exposed to water or chemicals, consider the specific corrosion resistance needed. Aluminum is ideal for marine environments, while copper performs better in industrial settings with exposure to chemicals or extreme heat.
Conclusion
Both aluminum and copper wire rope sleeves offer distinct advantages, but the best choice depends on your application’s specific requirements. For light-duty, cost-effective, and corrosion-resistant applications, aluminum wire rope sleeves are a solid option. For heavy-duty, high-strength needs where durability is critical, copper wire rope sleeves are the better choice.
By understanding these differences, you can ensure the safety, reliability, and longevity of your wire rope systems, no matter the industry or environment.
Looking for high-quality wire rope sleeves for your business? Contact us today to get a custom quote, explore bulk ordering options, and enjoy fast global shipping. Partner with a trusted supplier for all your wire rope accessory needs!
Contact our team at sales@qd-kailipu.com, Kailipu will work with you to make better Rigging, Lifting, Material handling products.