Types Of Webbing Slings
Polyester Webbing sling, also known as a web sling or lifting sling, is a piece of material made from synthetic fibers that is used in material handling and lifting operations. These slings are designed to securely lift, lower, or support heavy loads in a variety of industries, including construction, manufacturing, logistics, and more. Webbing slings are popular for their versatility, strength, and ease of use.
Eye and Eye Webbing Sling
Eye slings can generally be divided into two types: flat eye slings and twisted eye slings. A flat eye can be used in a choker hitch, basket hitch, or vertical hitch, while a twisted eye sling has eyes that are twisted 90° to form a better choker hitch. And what we currently use more widely is the flat eye sling, also known as a flat webbing sling or web sling.
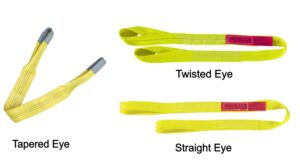
Endless Webbing sling
An endless webbing sling, also known as an endless loop sling or round sling, is a type of lifting and rigging equipment used to securely lift, lower, or support heavy loads in various industrial and construction applications. Unlike flat webbing slings that have reinforced loops at each end, endless webbing slings are endless webbing slings are constructed as continuous loops without any seams or joints.
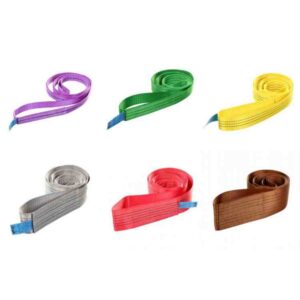
Round Webbing Sling
A round webbing sling, also known as a round sling or endless round sling. Unlike flat webbing slings or endless webbing slings, which have a flat or continuous loop design, round webbing slings are constructed as a continuous loop in a tubular, circular shape. And its outside is polyester woven tube sleeve, inside is multiple strands of fiber. So they’re ideal for a wide variety of applications including lifting, pulling, towing, etc.
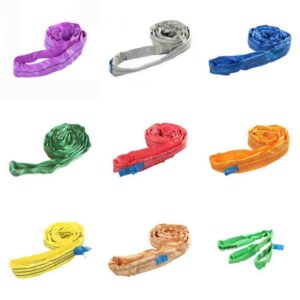
What Material Is Commonly Used For Web Sling?
Web slings are commonly made from synthetic materials that are chosen for their strength, durability, and resistance to environmental factors such as abrasion, chemicals, and UV radiation. The two most common materials used for web slings are:
Polyester Webbing Sling
Polyester web slings are known for their exceptional strength, low stretch properties, and resistance to UV radiation and moisture. They are often chosen for outdoor applications where exposure to sunlight and weather is a concern. Polyester web slings also have good resistance to mildew and rot. They are an excellent choice for heavy lifting operations and are generally less affected by acidic conditions compared to nylon.
Nylon Webbing Sling
Nylon web slings are a popular choice in various industries due to their excellent strength and versatility. They have a high tensile strength and resistance to abrasion, making them suitable for lifting heavy loads and enduring rough handling. Nylon web slings also have good resistance to chemicals and are less susceptible to mildew growth. However, they are sensitive to acidic environments.
Webbing Sling Materials: Nylon vs. Polyester
Both nylon and polyester web slings come in various configurations, including flat webbing slings, endless webbing slings, and round slings, to accommodate different lifting needs. The choice between nylon and polyester often depends on factors such as the specific application, environmental conditions, load capacity requirements, and user preferences.
What are the specifications of Polyester Webbing Slings?
The specifications of polyester webbing slings can vary depending on the manufacturer, type, and intended use. However, here are some common specifications and characteristics that you may encounter when dealing with polyester webbing slings:
The Appearance Of The Polyester Webbing Sling
The appearance of a polyester webbing sling can vary based on its design, width, length, and the manufacturer’s specifications. However, here are some common characteristics and elements of the appearance of polyester webbing slings:
1. The Color of Polyester Webbing sling
Polyester webbing slings come in various colors, with the most common being bright and vibrant, such as yellow, green, blue, orange, and red. The color of the sling can sometimes indicate its load capacity or working load limit (WLL), but color coding can vary between manufacturers.
2. The Width and length of Webbing sling
Width: The width of a polyester webbing sling can vary based on its capacity and intended use. Standard widths range from 1 inch to 12 inches or more. Wider slings generally have higher load capacities.
Length: Polyester webbing slings come in various lengths to accommodate different lifting and rigging tasks. Common lengths include 6 feet, 8 feet, 10 feet, and longer. Custom lengths may also be available.
3. Labels and Tags
Polyester webbing slings typically have labels or tags attached to them. These labels often include important information such as the working load limit (WLL), safety instructions, manufacturer’s information, and usage guidelines.
Technical Datas Of Polyester Webbing Sling
1. Understanding Working Load Limits (WLL) for Webbing Slings
Polyester webbing slings are rated for specific working load limits (WLL), which indicate the maximum load they can safely lift or support. WLLs are usually labeled on the sling and may be color-coded for easy identification. Common WLLs range from 1 ton (2,000 pounds) to several tons, depending on the sling’s width, length, and design.
2. What is webbing sling safety factor?
The safety factor is the ratio of the breaking strength of the sling material to the working load limit. Common safety factors are 5:1, 6:1 and 7:1, meaning the sling’s material has a breaking strength at least five or seven times higher than the WLL.
3. Temperature Range
Polyester webbing slings typically have a temperature range within which they can safely operate. This range may vary depending on the specific manufacturer and material used but often falls between -40°C (-40°F) to 100°C (212°F) or higher.
Webbing Sling Uses And Applications
Webbing slings are versatile tools used in a wide range of lifting, rigging, and securing applications across various industries. Their flexibility, strength, and resistance to environmental factors make them valuable for these purposes. Here are some common uses and applications of webbing slings:
1. Construction and Building Sites:
Lifting and positioning heavy construction materials, such as steel beams, concrete blocks, and roofing materials.
Securing loads to cranes, hoists, or other lifting equipment.
2. Manufacturing and Warehousing:
Moving machinery and equipment within a factory or warehouse.
Securing loads for storage or transportation.
3. Maritime and Shipping:
Securing cargo on ships and containers.
Handling and positioning ship rigging and equipment.
4. Agriculture:
Lifting and transporting large agricultural equipment.
Hoisting or positioning materials for farming operations.
5. Transportation and Logistics:
Securing and lifting loads on trucks, trailers, and shipping containers.
Handling and positioning cargo in logistics and distribution centers.
6. Mining and Quarrying:
Lifting and moving heavy mining equipment and materials.
Supporting conveyors and conveyor systems.
7. Utilities and Telecommunications:
Lifting and positioning utility poles, electrical transformers, and telecommunications equipment.
Safely securing loads for maintenance work.
8. Renewable Energy:
Installing and maintaining solar panels, wind turbines, and other renewable energy infrastructure.
9. Oil and Gas Industry:
Handling and positioning equipment and materials in offshore and onshore operations.
Securing loads during drilling and exploration activities.
10. Forestry and Logging:
Lifting and transporting logs and forestry equipment.
Supporting operations in remote and rugged terrain.
11. Rescue and Emergency Services:
Rigging systems for rope rescue and evacuation operations.
Providing support in technical rescue scenarios.
12. Military and Defense:
Handling and positioning military equipment and materials.
Supporting logistics and transport operations.
13. General Material Handling:
Lifting and moving heavy or awkward loads in industrial and commercial settings.
Tips for Inspecting and Maintaining Your Webbing Slings
Inspecting and maintaining webbing slings is crucial to ensure their safety and longevity. Regular checks help identify signs of wear, damage, or degradation that may compromise their integrity. Here are some tips for inspecting and maintaining your webbing slings:
1. Visual Inspection:
Before each use, conduct a visual inspection of the entire sling. Look for any signs of wear, cuts, abrasions, or damage on the webbing material.
Check for loose or damaged stitching, especially near the eyes and other load-bearing points.
Examine the sling for contaminants like oil, chemicals, or other substances that could weaken the material.
2. Labels and Tags:
Verify that the sling has legible and intact labels or tags. These labels typically contain important information such as the working load limit (WLL), safety guidelines, and usage instructions.
Ensure that any color-coding or safety tagging is in place and legible.
3. Eye Inspection:
Inspect the eyes or loops of the sling carefully. Look for fraying, tears, or any deformities that may weaken the attachment points.
4. Stitching Inspection:
Examine the stitching on the sling for any loose threads, broken stitches, or unraveling. Reinforced stitching is crucial for maintaining the sling’s strength.
5. Twists and Knots:
Check for any twists, knots, or kinks in the sling, as these can affect its lifting capacity and strength. Slings should lie flat without twists when in use.
6. Safety Factors:
Ensure that the webbing sling’s safety factor is within the specified range (e.g., 5:1 or 7:1). This factor represents the ratio between the sling’s breaking strength and its working load limit.
7. Load Compatibility:
Verify that the sling’s WLL is suitable for the intended load. Do not overload the sling, as it can lead to failure and accidents.
8. Environmental Factors:
Consider the environmental conditions in which the sling is used. For example, exposure to UV radiation, extreme temperatures, or corrosive substances can affect the sling’s material over time.
9. Record Keeping:
Maintain records of inspections, maintenance, and any incidents involving the sling. Keep track of the sling’s service life and retirement dates.
10. Training and Education:
Ensure that personnel involved in using and inspecting webbing slings are properly trained in safe lifting practices and sling inspection procedures.
Maintenance Tips:
Clean slings when necessary using mild soap and water. Rinse thoroughly and allow them to air dry. Avoid harsh cleaning agents that can damage the webbing material.
Store slings in a cool, dry, and protected area away from direct sunlight and sources of heat.
Avoid storing slings in contact with sharp objects or abrasive surfaces that could cause damage.
Replace any webbing sling that shows signs of wear, damage, or aging. Do not attempt to repair a damaged sling unless you have the appropriate training and equipment.
Regular inspections and maintenance are essential to ensure the safety and reliability of webbing slings in lifting and rigging operations. Always prioritize safety and follow manufacturer recommendations and industry standards.
Procurement And Considerations When Purchasing Webbing Slings
Procuring webbing slings requires careful consideration to ensure you choose the right slings for your specific needs and safety requirements. Here are some important considerations when purchasing webbing slings:
1. Identify Your Requirements:
Determine the type of lifting or rigging tasks you’ll be using the webbing slings for. Different applications may require specific types of slings (e.g., flat webbing slings, endless webbing slings, round slings).
Calculate the anticipated load capacity and working load limits (WLL) required for your tasks. The WLL should meet or exceed the heaviest loads you plan to lift or secure.
2. Select the Right Material:
Choose between nylon and polyester webbing slings based on the environmental conditions and specific needs of your application.
Consider factors such as resistance to UV radiation, moisture, chemicals, and abrasion.
3.Determine Sling Width and Length:
Select the appropriate sling width and length for your lifting tasks. Wider slings generally have higher load capacities.
Ensure that the length of the sling is suitable for your intended use, and consider the length needed for double wrapping or choker hitches, if applicable.
4. Safety Factors:
Understand the required safety factor for your application. Common safety factors are 5:1 and 7:1, indicating that the sling’s material has a breaking strength five or seven times higher than the working load limit (WLL).
5. Check Compliance with Standards:
Verify that the webbing slings you are considering comply with industry standards and regulations, such as those set by OSHA (Occupational Safety and Health Administration), ASME (American Society of Mechanical Engineers), and other relevant organizations.
6. Inspect Labels and Tags:
Ensure that each sling has legible labels or tags that provide essential information, including the WLL, safety instructions, and usage guidelines.
Verify any color coding or safety tagging.
7. Consider End Fittings:
Determine the type of end fittings or attachment points required for your tasks, such as eyes, hooks, or other hardware.
Ensure that the end fittings are suitable for your specific application.
8. Evaluate Manufacturer and Supplier Reputation:
Research and select reputable manufacturers and suppliers with a history of producing quality webbing slings.
Read customer reviews and ask for references if needed.
9. Price and Budget:
Compare prices from different suppliers, but avoid sacrificing quality and safety for lower costs. Focus on value rather than just the initial price.
10. Consider Environmental Conditions:
Account for the environmental conditions in which the slings will be used (e.g., exposure to sunlight, extreme temperatures, corrosive substances) and select slings that are suitable for those conditions.
By carefully considering these factors and conducting thorough research, you can make informed decisions when procuring webbing slings and ensure that you choose slings that are safe, reliable, and suitable for your specific lifting and rigging applications.
Sourcing Polyester Webbing sling From China
Sourcing polyester webbing slings from China can be a cost-effective option, but it requires careful planning to ensure product quality, compliance with standards, and a reliable supplier. To put it simply, clarify your needs including product positioning and budget, and then choose a reliable supplier. A good supplier can avoid many problems for you and better improve your procurement efficiency.
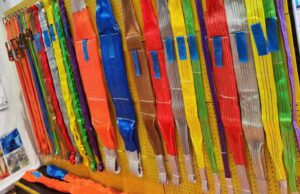
Contact a Reliable Rigging Equipment and Webbing Sling Supplier in China
In
rigging equipment, every component plays a vital role, because they are always a whole. As we always say, it is the most vulnerable part of the rigging equipment that determines its workload. Therefore it is crucial to find a reliable and experienced rigging equipment supplier during the procurement process. Qingdao Kailipu is a rigging equipment and webbing sling supplier integrating production and trade. With high professionalism and reasonable prices, it is one of the most professional one-stop suppliers of rigging components in the Chinese market. If you’re looking for a great polyester webbing sling supplier, let Kailipu be your first choice.
Browse our website or contact our team at
sales@qd-kailipu.com, Kailipu will work with you to make better rigging and lifting products.